Modified Sputter System
The desktop sputter coater system has been successfully repaired and modified to facilitate both dielectric and metal depositions, in addition to enabling etching capabilities. This compact and versatile setup transcends traditional limitations associated with home-brew fabrication, paving the way for groundbreaking research endeavors.
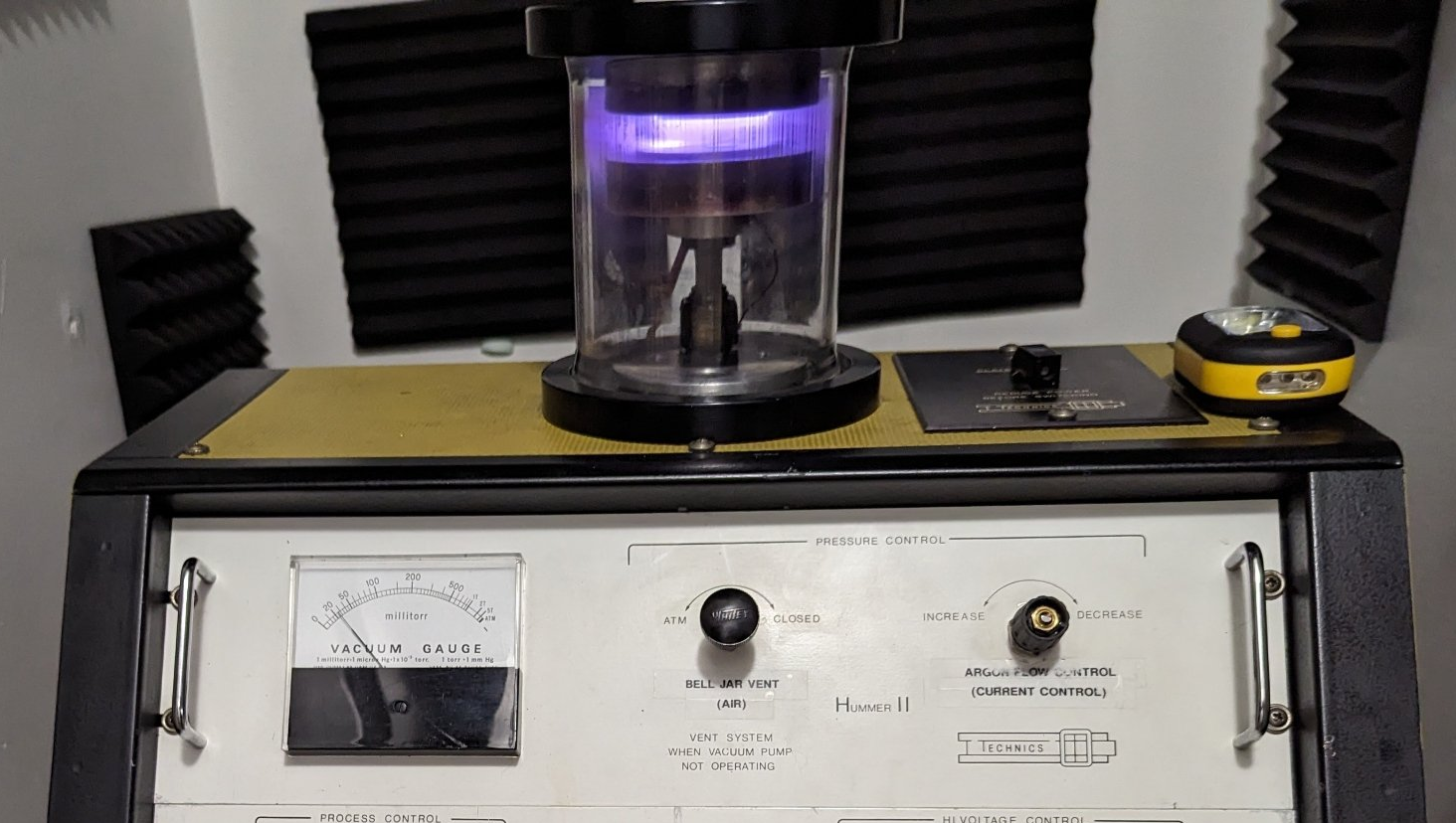
I acquired a Hummer II sputter system, an older desktop sputter coater previously employed for SEM sample coatings. Originally, the unit operated on a rough pump, connected to the main chamber through basic tubing. Although simple in design, this sputter coater stands out due to its capability to power the sample electrode, thereby enabling etching as opposed to the conventional DC sputtering of the target. The unit can accommodate 2" targets, establishing a bias between a grounded outer ring and the opposite plate holding the sample.
Upon arrival, the system was non-operational and necessitated some repair work to become functional. I sourced Argon from a local welding supply shop, and employed wall sound insulation to ensure quiet operation. Initially, the system could only coat low-reactive metals like gold or silver due to its low vacuum nature. To expand the range of sputter-able materials, I replaced the existing rough pump within the unit's base. Subsequently, I acquired an Edwards turbo pump, fabricated a controller box for it, and integrated it with the chamber base plate, securely affixing the turbo to the chassis. To mitigate overheating during extended deposition sessions, a water cooling system was added to the unit.
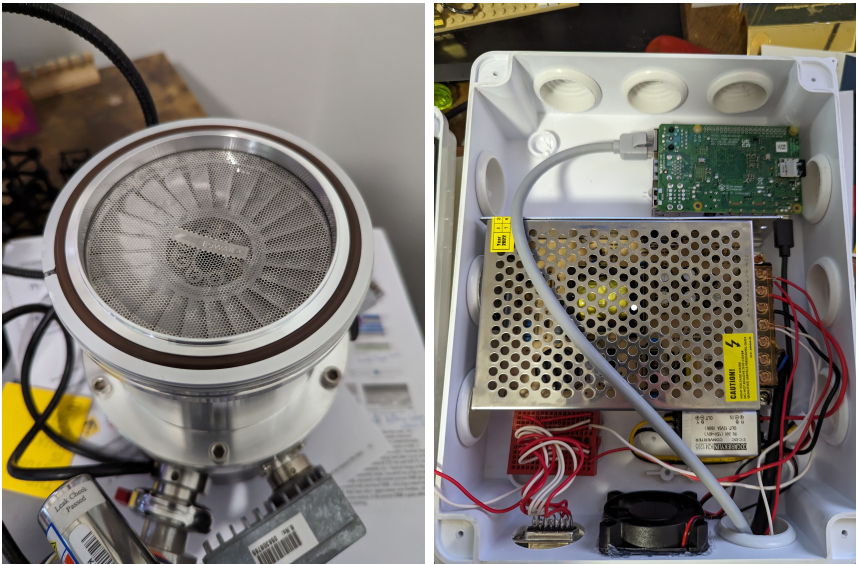
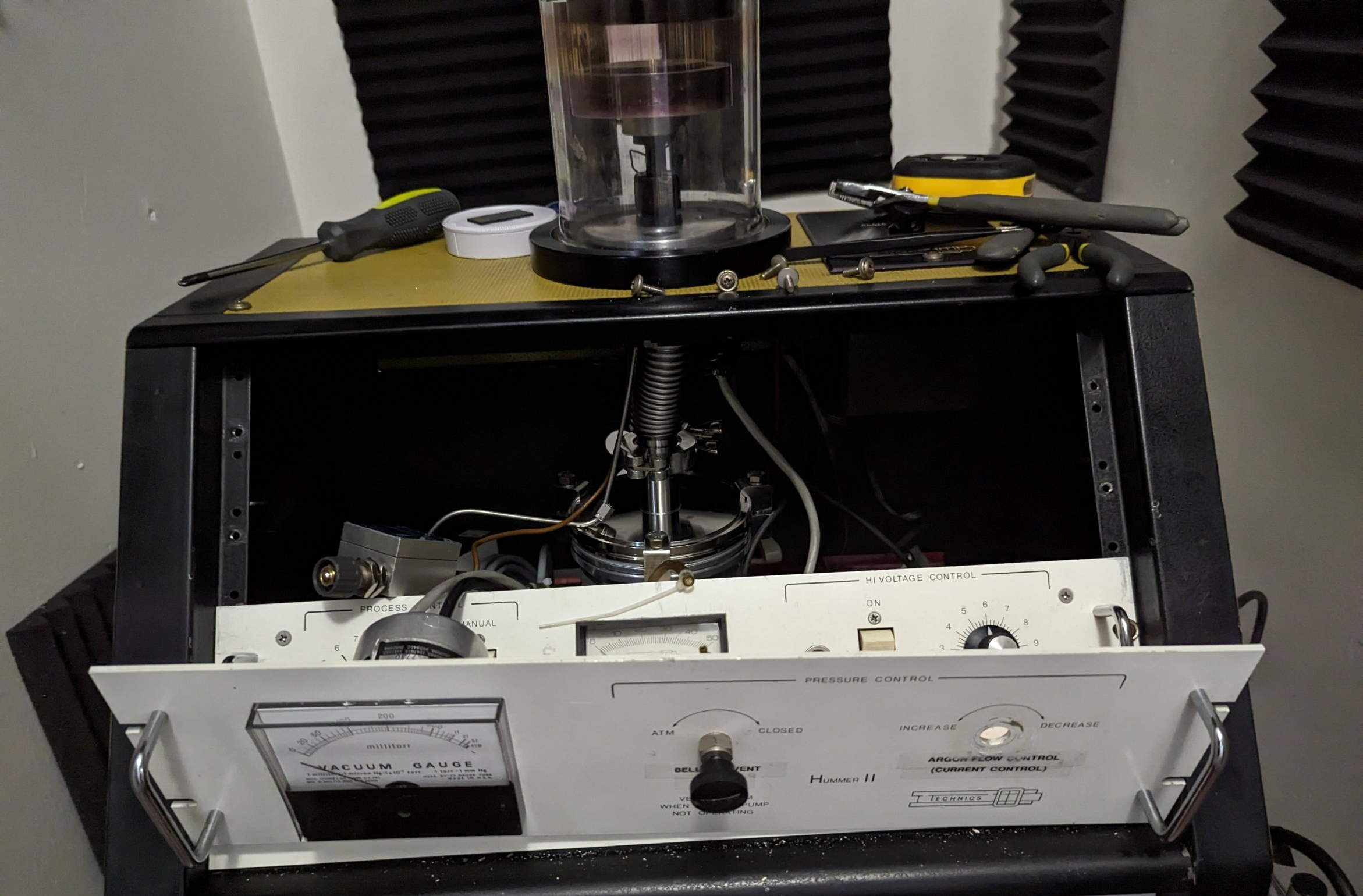
The in-built thermocouple gauge, dependent on the gas conductance within the chamber, is ineffective under higher vacuum molecular flow conditions, necessitating an additional gauge. I procured a cold cathode gauge online, rectified a short circuit issue, and installed both the gauge and unit. The top of the unit is aligned flush with the top of the unit, maintaining its compact design.
With the turbo pump in place, the system could deposit a broad spectrum of materials without excessive oxygen reactions, including doped Silicon, Nickel, Titanium, and Silver. Conversely, operating without the turbo pump allowed for reactive sputtering in the presence of residual oxygen. Silicon Dioxide and Nickel Oxide films were successfully deposited and analyzed via EDX. These dielectric and wide bandgap material depositions are instrumental in advancing process steps and opening new avenues for research. Preliminary etching experiments using both Argon and Oxygen plasmas have been conducted; while Oxygen proved effective for photoresist ashing and wafer cleaning, Argon etching, though viable, resulted in some surface damage and poor selectivity. The etching performance can potentially be enhanced through the use of alternative gases like SF6, which is readily available.
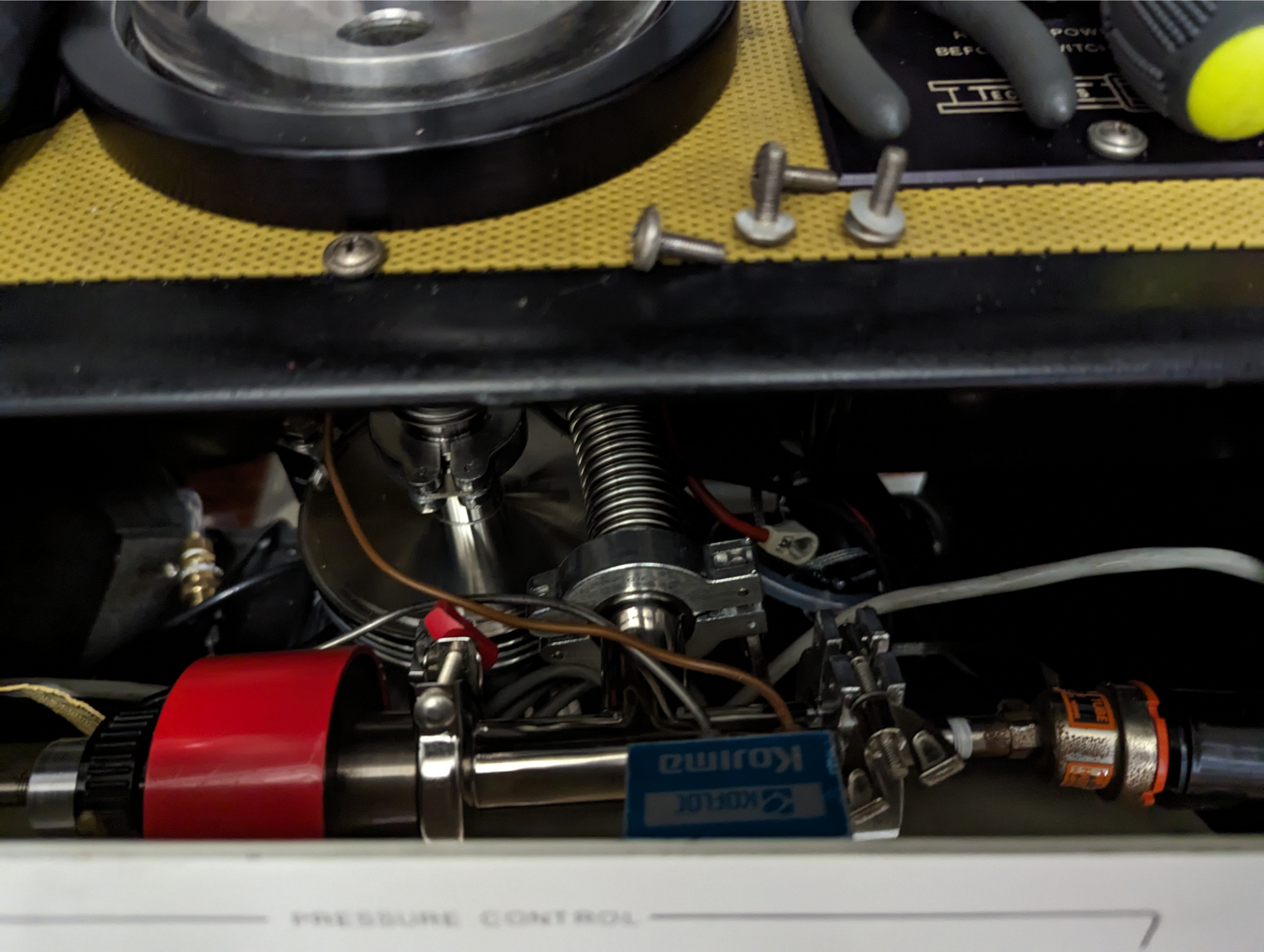
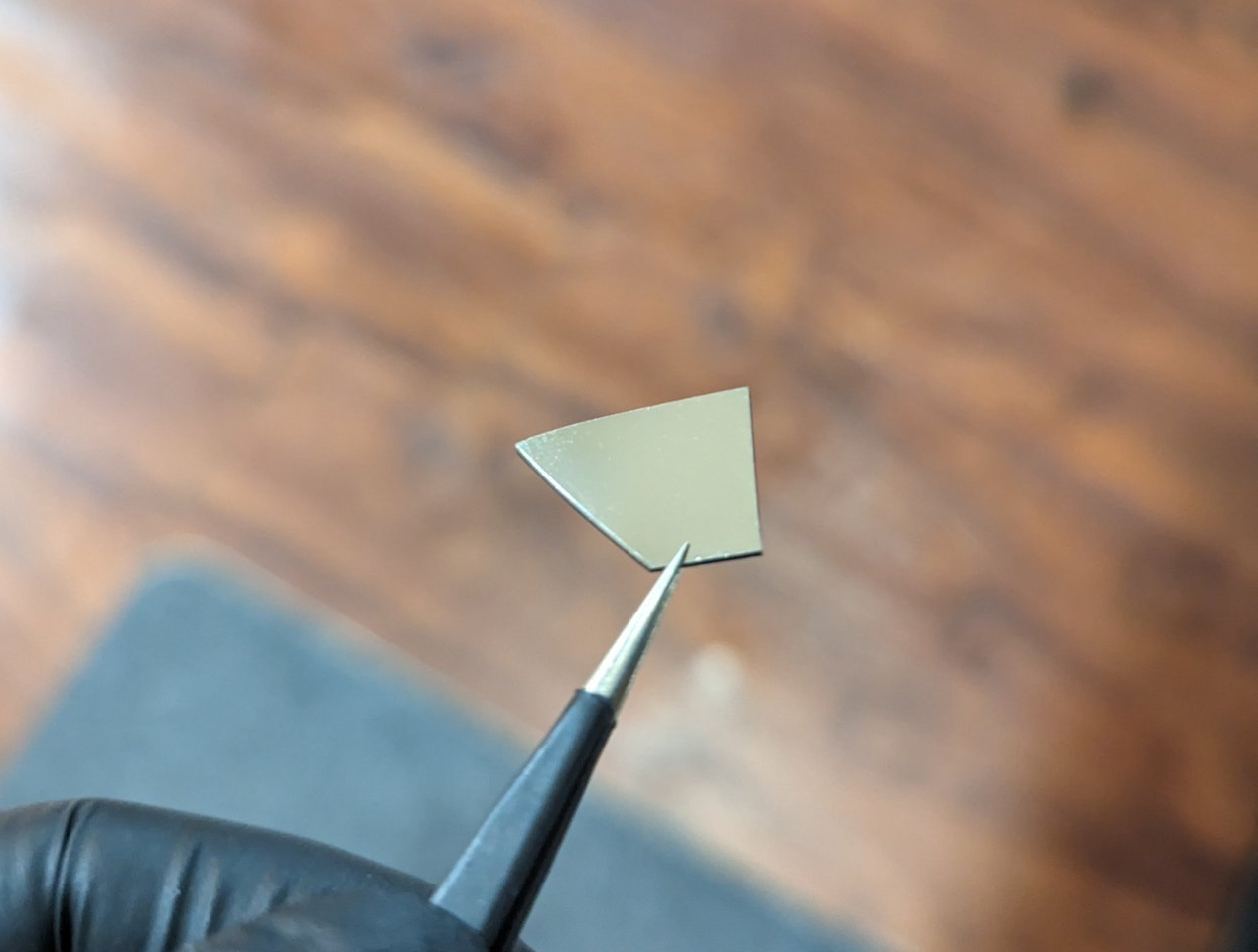
This upgraded sputter system embodies a cost-effective and compact research setup, albeit with a few areas earmarked for further improvements. For instance, the center electrode designed to hold the sample wasn't tailored for high vacuum operation, causing a minor leak. Additionally, the current base plate offers limited attachment options, requiring the incorporation of a T-junction and bellows for the gauges. To address these issues, a new base plate featuring an improved sealing mechanism has been designed and is currently under fabrication.
Future plans for this system encompass homebrew transistor fabrication and extensive research on wide band-gap materials.